Shell Type Transformer | A Complete Guide
Table of Contents
Introduction
In the field of electrical engineering, transformers are essential in facilitating the efficient transmission and distribution of electrical energy. Among the different types of transformers, the Shell Type Transformer is important due its configuration and specific applications. For this article, we will take an in depth look at the shell type transformer’s construction, advantages, disadvantages and specific applications today’s electrical systems.
Shell Type Transformers
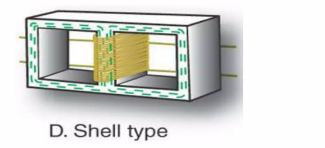
1.1 Definition
A Shell Type Transformer is defined by the arrangement of its core, with the windings surrounded by the core in a shell type arrangement. This is in contrast to the core type transformer in which the windings surround the core.
Construction Details
The core of a shell type transformer consists of three limbs, a center limb and two outer limbs. Both the primary and secondary windings are placed on the center limb and the magnetic flux returns through the outer limbs. The result is a double magnetic circuit and more efficient transformer. The windings are in the form of a sandwich or disk of essential high voltage and low voltage windings. This minimized leakage reactance which improves voltage regulation.
Benefits of Shell Type Transformers
2.1 Increased Short-Circuit Strength
The structure of the shell type allows for greater overall mechanical strength against the forces associated with short-circuit phenomena. The core completely encloses the winding so there is good support offered by the core, which ensures the windings have reduced propensity to distort when fault conditions occur.
2.2 Less Leakage Flux
The sandwich winding arrangements mean the magnetic flux is entirely contained in the core and, consequently there is less leakage. Reduced leakage in turns increases efficiency and voltage regulation.
2.3 Smaller Size
Shell type transformers are generally smaller than core type transformers. Effective use of iron and symmetrical windings provide an excellent transformer ‘footprint’, or enclosure volume.
2.4 Improved Cooling
Cooling is more effective as designed because shell windings can be cooled using oil immersion or cooled air forced on the windings. Windings are close to the core so heat dissipation is also effective.
Shell Type Transformers: Disadvantages
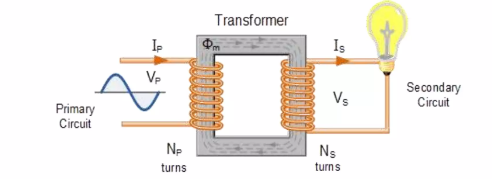
3.1 Complexity of Construction
Shell type transformers are designed in a complex way, which means more difficult construction. Since the design encloses the windings with the core, more precision is required during assembly, extending manufacturing time and cost.
3.2 Natural cooling at 30% Less effectiveness
The design facilitates cooling, but natural cooling is not as effective as in core type transformers and would require large units to have additional cooling means.
3.3 Maintenance Difficulties
With the core still surrounding the windings in the shell-type construction, it can be difficult to gain access to the windings for repair. Accordingly, servicing time would be lengthened based on the time it takes to properly gain access to the enclosure.
Uses of Shell Type Transformers
4.1 Low Voltage Applications
Shell type transformers are often used in low voltage applications which include electronic circuits and control systems due to their small size and efficient operation.
Power Distribution
Shell type transformers are used in power distribution systems as they offer excellent voltage regulation and mechanical strength, especially in urban distribution where space is often limited.
Industrial Use
Industries make use of shell type transformers for certain applications which require used with stable voltage and robust performance, such as manufacturing machinery and processing plants.
Considerations for Design
6.1 Core Material
Generally, laminated silicon steel is used for the core to reduce eddy current loss. The laminations must be insulated from each other to minimize energy loss through eddy currents.
Winding Configuration
The use of sandwich-wound structure is important in connection with leakage reactance. Sufficient insulation between layers of windings must be employed to isolate short circuits, and to ensure a long life.
6.3 Cooling Methods
The types of cooling depend on the application. Cooling methods can be natural convection, forced air or oil-immersed cooling. The type chosen depends on the size of transformer and anticipated environment.
Maintenance and troubleshooting
Routine Inspections
Routine inspections are essential for the continued life and reliability of shell type transformers. Inspections reveal early signs of failure or deterioration such as hot spots, loose connections or insulation decay, before they cause a significant failure. Inspectors often have a predominantly visual inspection process, but will also assess the transformer visually, thermographically and mechanically for proper integrity and operations and avoid critical outages.
One type of inspection that is particularly useful in shell type transformers is infrared thermography to detect any hot spots in transformer components. Common hot spots signal higher resistance connections or poor load balancing between windings. Early detection will allow the operations to schedule maintenance in an appropriate time frame, avoid unsafe conditions and increase the operational capability of shell type transformers.
Oil Analysis
For oil-immersed shell-type transformers, analyzing the oil is critical in assessing internal conditions. The oil is the dielectric fluid (or an insulating fluid) that acts as an insulator and a cooling medium, so the quality of the dielectric fluid is always important. Parameters such as moisture, acidity and dielectric strength, in addition to many other analysis parameters, are used to look at the aging/failure of transformers.
Advanced oil testing involves Dissolved Gas Analysis (DGA). DGA helps in determining gases generated as a result of insulation degradation or arcing within transformers. The presence and concentration of dissolved gases indicate fault conditions, such as partial discharges, overheating, and electrical arcing. Oil analysis is essential to predictive maintenance programs for transformers by reducing downtime and improving transformer longevity.
Cleaning and Tightening
Cleaning and tightening should be considered the most fundamental, but inescapable, maintenance of shell type transformers. Insulating surfaces and terminal connections can be victims of dust, dirt and moisture over time. This form of contamination can decrease insulation resistance and may cause tracking or flashover, a dangerous situation for equipment and personnel alike.
In addition, ensuring that all electrical connections are tight and free of corrosion can help to eliminates overheating due to poorly maintained connections, as well as voltage drops or mechanical failures. Poor maintenance practices such as loose bolts and oxidized contacts can endanger proper transformer operation and create dangerous situations while in use. Simply cleaning and tightening on a routine basis is an important way to avoid unwanted or unexpected breakdowns, while maintaining the transformers’ greatest usable lifespan.
Upcoming Trends
The outlook for Shell Type Transformers includes:
Smart Transformers: The incorporation of sensors and IoT capabilities for real-time diagnostic and predictive maintenance.
Sustainable Designs: Consideration of biodegradable insulating fluids and recyclable materials.
Advanced Materials: Continued exploration of magnetic materials with improved magnetic properties and lower losses.
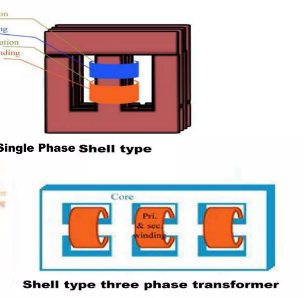
Conclusion
Shell Type Transformers play a crucial role in modern electrical systems, offering advantages like compact design, enhanced mechanical strength, and efficient performance in specific applications. While they come with certain challenges in construction and maintenance, ongoing advancements are addressing these issues, making Shell Type Transformers a viable choice for various applications.
FAQS
- Defining a Shell Type Transformer
A Shell Type Transformer is a type of transformer where the core surrounds the windings and has a shell-like design. They use a double magnetic circuit, allowing for a more efficient transformer with reduced leakage flux in the iron core, making them suitable for high-performance or industrial applications. - How does a Shell Type transformer differ from a Core Type transformer?
The main influence is core design:
Core Type Transformer – the windings are wrapped around the core limbs of the metallurgical core.
Shell Type Transformer – the core encloses the physical windings, providing better mechanical robustness and leakage. Shell types typically power high-voltage and critical systems while core types are used more commonly in distribution systems or lower voltage levels.
- Core of a Shell Type Transformer
A Shell Type Transformer Core is made with laminated steel sheets with an “E-I” or “E-E” shape. The winding is placed on the center limb, and the outer limbs complete the magnetic path, forming two parallel magnetic circuits, providing better magnetic flux distribution.
What is a Shell Type Transformer?
Shell type transformers consist of a central limb for windings, and two outer limbs as alternative paths to complete the magnetic circuit. The windings are arranged in a sandwich (high-low-high) configuration in order to minimize the leakage reactance. The core encloses all of the windings and provides additional core protection with greater mechanical stability as well as increased magnetic efficiency.
- Shell Type Transformer versus Core Type: Which is Better?
An ultimately depends on the application.
Shell Type: Better short-circuit strength, more compact, and reduced leakage flux makes it ideal for industrial uses and critical infrastructure.
Core Type: More simple, lighter, and easier to cool makes it ideal for general distribution.
For mechanical strength and regulation, shell type will generally out-perform a core type transformer.
- What is a 3-Phase shell type transformer?
A 3-phase shell type transformer is a transformer that has three sets of windings in a shell-type core configuration. The three-phase design allows for more uniform magnetic flux, reduces phase-to-phase interference, and provides greater mechanical durability, making it better suited for use in large scale industrial applications and the power grid. - Is there a Shell Type Transformer Diagram?
A typical shell type transformer diagram